5251 and 5182 Aluminum Sheet Properties
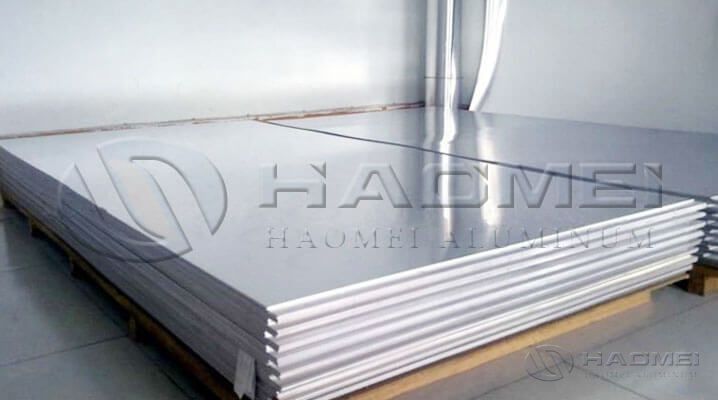
5251 aluminum is a medium strength alloy, featuring rapid work hardening and ease of welding. 5182 aluminum has good stamping performance and tensile strength. They both have good corrosion resistance. Learn more.
5251 aluminum is a medium strength alloy that has good ductility and therefore good formability. Alloy 5251 is known for its rapid work hardening and ease of welding. It also has high corrosion resistance, especially in marine environments.
The common alloys for spinning include 1050, 1060, 1070, 3003, 5052, 5251, 6061, and 6063. The hardness of aluminum is divided into three types: soft, semi-hard and hard. Under the same condition, the hardness, tensile strength, and elongation of the above aluminum alloys increase in sequence.
1050, 1060, and 1070 are often used in lighting lampshades and are easy to undergo surface treatment processes such as anodizing and painting. 3003 aluminum has the best tensile strength and is suitable for stretch forming processes.
5052 and 5251 are often used in auto parts. After spinning, the products have greater strength and good corrosion resistance. 6061 and 6063 have the highest strength and hardness. They are often used in building hardware and are also suitable for surface anodizing.
Main tempers of 5251 alloys
5251-H24: It is work hardened by rolling, then annealed to semi-hard.
5251-H26: It is work hardened by rolling, then annealed to three-quarters hardness.
5251-O: soft
5251-H22: It is work hardened by by rolling then annealed to one quarter hard.
Welding performance of 5251 aluminum sheet
When 5251 aluminum is welded to itself, 6xxx aluminum alloys, 7xxx aluminum alloys and most other 5xxx aluminum alloys, the recommended aluminum welding wire is 5356. When it is welded to 5005, 5020, 1XXX series or 3XXX series alloys, the recommended filler wire is 4043.
Physical properties | Value |
Density | 2.69 g/cm3 |
Melting point | 625℃ |
Thermal expansion | 25x10^-6/K |
Elastic modulus | 70 Pa |
Thermal conductivity | 134W/mK |
Resistivity | 0.044 x10^-6 Ω .m |
The main element of aluminum-magnesium alloy is aluminum, and a small amount of magnesium or other metal materials is added to strengthen its hardness. Aluminum alloys with Mg as the main added element are also called rust-proof aluminum alloys because of their good corrosion resistance. Because it is metal itself, its thermal conductivity and strength are particularly outstanding.
Aluminum alloy inner panels for automobiles usually choose 5052 and 5182 aluminum alloys. In terms of deep drawing performance and tensile strength, 5052 aluminum alloy is far less good than 5182 alloy. Therefore, the preferred aluminum alloy for stamping the complex inner panels is 5182 aluminum sheet.
Features
1. Good corrosion resistance: 5182 aluminum alloy is added with elements such as magnesium and silicon to give it good corrosion resistance and can be used for a long time in humid or acidic environments.
2. Excellent formability and processing performance: 5182 aluminum alloy has good formability and can be used to manufacture various complex-shaped automobile shell parts by stamping, drawing, deep drawing and other processing methods. At the same time, the aluminum alloy also has excellent processing properties and is convenient for cutting, welding and other processing operations.
3. High strength and toughness: 5182 aluminum alloy has high strength and excellent toughness, high tensile strength and yield strength, and can effectively protect the safety of the passengers even in severe situations such as high-speed collisions.
4. Lightweight: Compared with traditional steel, 5182 aluminum alloy has a lighter weight, so it can effectively reduce the weight of the vehicle and improve the fuel economy and driving performance of the vehicle.
Inquiry
TABLE OF Contents

Haomei Aluminum CO., LTD.
Tel/Whatsapp: +86-15978414719
Email: sale@alumhm.com
Website: https://www.alumhm.com
Xin'an Industrial Assemble Region,Luoyang,Henan Province,China
Office Add: 1103, No.14 Waihuan Road, CBD, Zhengzhou, China