Aluminum 1100 1050 H14 Properties
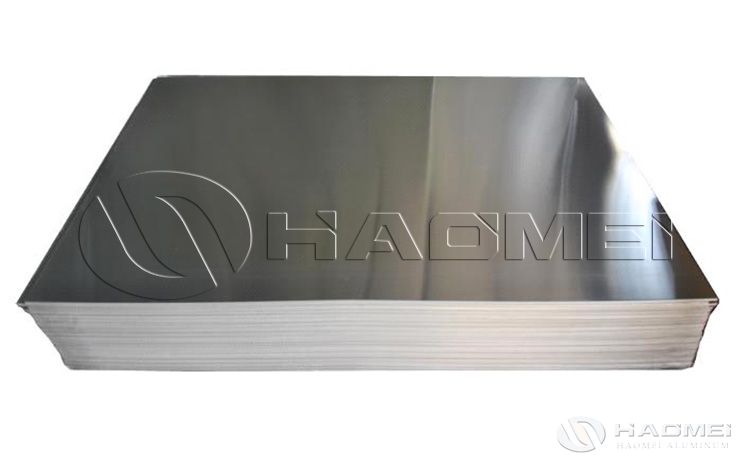
1050 aluminium sheet is formed by adding a small amount of other elements to pure aluminum. Its aluminum content is as high as 99.50%, silicon (Si) content ≤0.25%, copper (Cu) ≤0.05%, magnesium (Mg) ≤0.05%, zinc (Zn) ≤0.05%, manganese (Mn) ≤0.05%, titaniu
1050 aluminium sheet is formed by adding a small amount of other elements to pure aluminum. Its aluminum content is as high as 99.50%, silicon (Si) content ≤0.25%, copper (Cu) ≤0.05%, magnesium (Mg) ≤0.05%, zinc (Zn) ≤0.05%, manganese (Mn) ≤0.05%, titanium (Ti) ≤0.03%, vanadium (V) ≤0.05%, and iron (Fe) content is 0.000 - 0.400%. Such chemical composition gives 1050 aluminum alloy excellent forming and processing characteristics, high corrosion resistance, good weldability and conductivity.
1100 aluminum alloy is also based on high-purity aluminum, with an aluminum content of 99.00%. The total amount of silicon and iron (Si + Fe) is 0.95%, the copper (Cu) content is 0.05-0.20%, the zinc (Zn) is 0.10%, and the manganese (Mn) is 0.05%. The reasonable ratio of these elements gives 1100 aluminum alloy good ductility, formability, weldability and corrosion resistance, and after anodizing, its corrosion resistance and appearance can be significantly improved.
Physical properties
The density of 1050 h14 aluminium is about 2.71g/cm³, the melting point ranges from 646 to 657℃, the conductivity is 61.3% IACS at 20℃ (68℉), and the resistivity is 0.0281Ωmm²/m at 20℃ (68℉).
1100 aluminum alloy is close to 1050 in this respect, with a density of about 2.71g/cm³ and a conductivity of 55-63% IACS at 20℃ (68℉). Their good electrical conductivity makes them have the potential for wide application in the electronics field.
Mechanical properties
The tensile strength of 1050 h14 aluminum is 95-130MPa, and the elongation δ≥ 3-6%. That of aluminum 1100 h14 is 125MPa, the yield strength is 115MPa, the hardness (500kg force 10mm ball) is 32, the elongation (1.6mm thickness) is 10%, and the maximum shear stress is 50MPa.
Overall, the strength of both is relatively low, but they have certain ductility, which can meet some processing requirements that do not require strict strength but have requirements for formability.
Chemical properties
Both aluminum alloys have good corrosion resistance. Due to its chemical composition, 1050 aluminum alloy can remain stable under normal conditions. After anodizing, a dense oxide film is formed on the surface of 1100 aluminum alloy, which further improves its corrosion resistance and can be used in more complex environments. For example, in some chemical equipment, food industry equipment and storage containers, this corrosion resistance is particularly important.
Main applications
1050 aluminum alloy is widely used in products with low strength requirements. In the manufacture of chemical instruments, various reactors, pipelines and other parts can be made due to its corrosion resistance and good processing performance.
In terms of welding parts and heat exchangers, the weldability and thermal conductivity of 1050 aluminum alloy play an important role. For clock surfaces, dials, nameplates, etc., 1050 aluminum alloy can provide good surface quality and certain weather resistance. In addition, it can often be seen in daily necessities such as kitchen utensils, decorations, and reflective appliances.
The application field of 1100 aluminum alloy is also very wide. In chemical equipment, its corrosion resistance and formability make it an ideal material for making various containers and pipes. In terms of food industry equipment and storage containers, 1100 aluminum alloy meets food hygiene and safety standards, and has good corrosion resistance, which can ensure the safe storage of food.
Inquiry
TABLE OF Contents

Haomei Aluminum CO., LTD.
Tel/Whatsapp: +86-15978414719
Email: sale@alumhm.com
Website: https://www.alumhm.com
Xin'an Industrial Assemble Region,Luoyang,Henan Province,China
Office Add: 1103, No.14 Waihuan Road, CBD, Zhengzhou, China